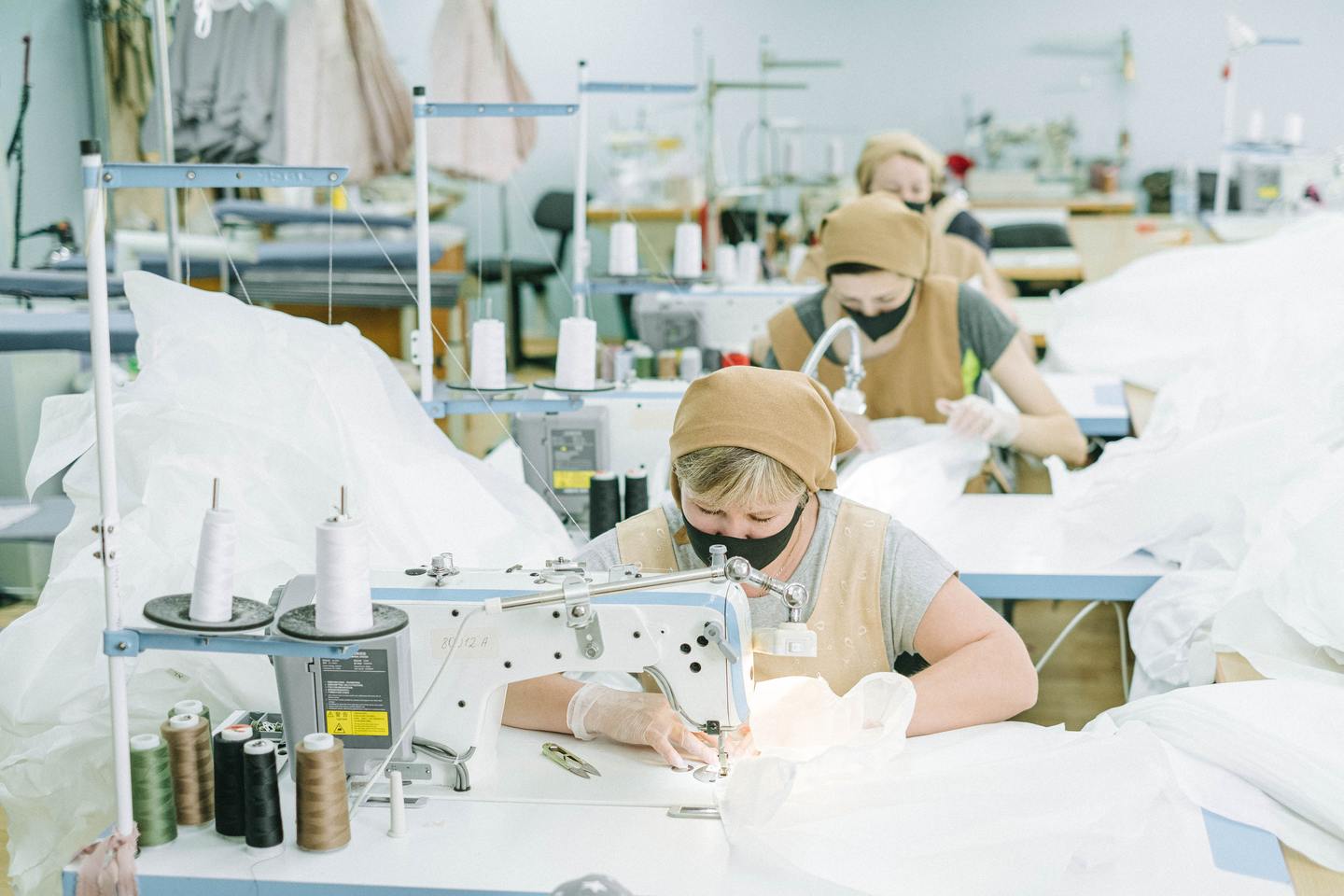
Have you ever marveled at the seamless coordination between machinery and the workforce in some of the most successful manufacturing plants? What’s the secret behind ensuring that every component is flawlessly assembled and each product is meticulously quality-checked while also maintaining a happy and motivated workforce? The answer lies in the art of effective Labor Management, which plays a pivotal role in manufacturing success with labor management.
Imagine a dynamic shop floor teeming with activity-skilled workers skillfully navigating their way around cutting-edge machinery, and production lines operating in perfect harmony. All of this is choreographed by an invisible conductor, a master of labor management, who is armed with Real-Time Insights into Labor Management.
But this isn’t just about meeting production quotas and reducing operational costs; it’s about orchestrating a symphony in which every worker plays a crucial role in the grand performance of Manufacturing Success through Labor Management. And the story doesn’t end here.
Intrigued? Let’s take a closer look. We’ll delve into a realm of strategies designed to enhance productivity through the integration of ERP systems, methods to efficiently manage small-scale manufacturing enterprises, and approaches to address wage disparities within your organization. As we explore these avenues, you’ll uncover the intricate workings that transform a manufacturing plant into a harmonious orchestra of success.
Table of Contents:
- The Role of Labor Management in Manufacturing Success
- Strategies for Enhancing Labor Productivity
- Diversity and Inclusion in the Manufacturing Industry
- The Influence of Labor Unions on Manufacturing
- Managing Labor Costs for Small Businesses in Manufacturing
- Technology’s Role in Streamlining Labor Management
- FAQs in Relation to Manufacturing Success With Labor Management
- Conclusion
The Role of Labor Management in Manufacturing Success
With 12.8 million people currently employed, the manufacturing industry has been a significant contributor to job creation, adding another 22,000 employees in 2023 alone.
Labor management plays a pivotal role here by ensuring the effective use of this substantial workforce. From managing labor costs at manufacturing plants to fostering labor-management partnerships – these aspects are vital for achieving success on the shop floor.
A key component is tracking labor productivity which can significantly impact customer service and ultimately meet customer demands. It involves monitoring various parameters such as time spent on each task or project, employee performance against set goals, and efficiency in handling resources effectively.
This doesn’t just apply to large-scale operations but also to small businesses within the sector that need strategic labor management approaches tailored specifically for them. With tools like ERP solutions aiding data collection and attendance tracking systems streamlining workflow processes – it’s about making every second count towards overall output quality.
Labor-Management Partnerships: A Pillar of Strength
Fostering strong business relationships between managers and workers leads to enhanced community engagement at all levels of an organization’s labor force.
National Labor Relations Board reports showing how productive negotiations can lead not only toward improving working conditions but also aid with compliance audits mandated by executive orders—making sure everyone abides by stipulated regulations while maximizing production capacities through mutual understanding and respect for individual rights at workstations around factories nationwide.
“A healthy partnership is where both parties bring something valuable – managers bring structure & planning whereas employees provide skill & creativity.”
Tackling Costs: The Balance of Quality and Quantity
Managing labor costs involves a delicate balance between ensuring a quality workforce and keeping an eye on the bottom line. It’s not just about cutting corners but creating employee value, improving performance through constructive feedback, and making strategic job classifications that benefit both workers and the company.
costs is a delicate balancing act. The struggle is real, but smart strategies can help businesses thrive even in tough times. And that’s where the need for efficient labor management comes into play.
Thriving in the manufacturing sector calls for strategic labor management. This includes effective cost control, fostering strong relationships between managers and workers, tracking productivity meticulously with tools like ERP solutions, and maintaining compliance with regulations. A successful balance lies in creating employee value while improving performance and adhering to the bottom line.
Strategies for Enhancing Labor Productivity
Manufacturing success hinges on labor productivity. But how can we boost it? One proven strategy is through data collection and analysis.
Astonishingly, only 13.2% of manufacturing plants have implemented ERP systems. These platforms gather crucial information in real-time, allowing leaders to make immediate decisions based on hard facts. This approach enables managers to track labor costs effectively, spot inefficiencies swiftly, and devise solutions promptly.
Utilizing ERP Solutions for Improved Productivity
The world moves fast; so should your decision-making process. Manufacturers are under pressure not just to deliver products within their lead times but also to offer greater variability based on customer order configurations. Sounds like a tough task?
An Enterprise Resource Planning (ERP) system might be the answer you’re looking for. These systems let manufacturers optimize employee performance by providing timely feedback and training opportunities while offering a holistic view of operations – all at once.
You may wonder if investing in such technology will pay off or even ask why less than one-sixth of plants use these tools. Here’s an analogy: It’s akin to driving a car without GPS—you’ll get there eventually but with unnecessary detours and delays.
Consider this – each misstep costs money; every delay disrupts supply chains further down the line impacting customer service adversely. Therefore adopting technologies that streamline processes becomes critical not just for survival but more importantly—for thriving—in today’s cutthroat business environment.
Diversity and Inclusion in the Manufacturing Industry
The manufacturing industry is traditionally a male-dominated field. But, let’s face it – diversity is an area where improvement is needed. The Manufacturing Institute reveals that 79.5% of workers are White, showing a significant lack of diversity.
Gender inequality also exists with clear salary inequity between men and women prevalent within the sector. Why should this matter to us? Well, diverse teams bring more perspectives to problem-solving sessions leading to innovative solutions.
The aging workforce remains another concern for the manufacturing industry. The average employee falls into older Gen X or younger millennial categories implying an imminent skills gap as these employees start retiring.
Nurturing Diversity for Better Results
In order to build robust labor management strategies, organizations need to ensure they are harnessing all available talent irrespective of their age, gender, or race.
This not only helps companies mirror their customer base better but also contributes towards creating more inclusive work environments which lead to improved productivity levels and increased profitability over time.
Moving Towards Equity
Fighting salary disparity can be challenging but ensuring fair pay practices based on skill level rather than demographic factors like gender can make sure businesses attract top-notch talents from various backgrounds thus enhancing overall competitiveness in the marketplace.
If you ask me personally though – I’d say: Hey folks. It’s high time we shook things up around here.
The Influence of Labor Unions on Manufacturing
Labor unions have a significant role to play in the manufacturing industry. Their influence extends from shaping labor management strategies to impacting overall productivity.
State of Unionization and its Impact on Labor Management
Recently, union membership has been declining gradually. But, contrary to what one might expect, this hasn’t dampened their resolve. In fact, labor unions are ramping up union organizing efforts as they adapt and evolve within the changing landscape of the manufacturing industry.
This decline in union membership poses unique challenges for both parties involved. For manufacturers, it means navigating through changes with respect to employee rights and working conditions while also balancing customer demands. On the other hand, reduced union strength can lead some workers to feel underrepresented or neglected – creating an environment ripe for discord if not managed carefully.
So how does all this impact labor management? It’s quite simple really: strong unions typically translate into better working conditions which could boost worker morale and consequently enhance productivity levels on shop floors. That said, however, the increasing focus on community engagement by many manufacturers suggests that even without strong unions, positive results can still be achieved.
To achieve success, it is important to understand the relationship between labor relations boards such as the NLRB and various stakeholders. Remember – every change presents new opportunities; knowing how best to leverage them is key.
Managing Labor Costs for Small Businesses in Manufacturing
Manufacturing firms, particularly those with fewer than 20 employees—which make up a staggering 74.3% of the sector—face unique challenges when it comes to managing labor costs. As employment projections indicate a decline of approximately 139,400 people from 2023 to 2031 according to U.S. Census Bureau data, effective strategies become even more vital.
The first step is tracking labor effectively. Accurate record-keeping allows you to see where your money goes and helps identify areas for improvement. The use of ERP solutions can streamline this process by automating time collection and providing real-time information that aids decision-making.
A key component here involves creating employee schedules based on their skills and job classifications, rather than merely filling slots randomly or traditionally—a move-the-needle mindset that reduces wastage while ensuring high-quality output.
Strategies for Managing Labor
Beyond tracking, active management of labor requires strategic thinking about workforce management. This might mean cross-training workers so they can handle multiple roles—increasing flexibility while reducing downtime—or developing performance-based incentives designed not just to encourage hard work but also to foster loyalty among skilled workers in an increasingly competitive market.
An often overlooked yet crucial strategy is nurturing business relationships through community engagement—an investment in goodwill that translates into a quality workforce committed not only towards achieving manufacturing success but also building lasting value within their communities.
The Role of Employee Engagement
In small businesses especially, every team member plays an integral part; hence keeping them engaged should be at the heart of any successful labor-management strategy—the goal being more than just managing labor costs, but enhancing overall productivity and meeting customer demands.
Employee engagement involves open communication channels where feedback is not only given but valued. Regular performance reviews that highlight strengths while addressing areas of improvement play a pivotal role here as well—after all, employees who feel heard are more likely to stay committed in the long run.
Small manufacturing firms need to nail labor management for success. Track costs accurately, schedule smartly based on skills, and use ERP systems to automate time collection. Don’t just manage your workforce—engage them through cross-training, performance incentives, community engagement initiatives, and open communication channels that value feedback.
Technology’s Role in Streamlining Labor Management
The manufacturing industry is continually evolving, with technology playing a pivotal role. One key area where this transformation is evident lies within labor management.
Today, manufacturers are increasingly turning to technological solutions like ERP systems. These integrated software platforms allow businesses to manage and automate many aspects of their operations – including labor management. ERP systems help companies streamline processes by providing real-time information for immediate decision-making.
ERP Integration and Labor Management
In the world of manufacturing, it’s shocking that only 13.2% of plants have implemented ERP systems so far. There’s a huge opportunity here waiting to be seized.
An effectively deployed ERP system can provide detailed insights into workforce productivity levels on the shop floor. This kind of visibility allows managers to quickly respond to changes in customer demands or working conditions – no more guessing games.
Automated time collection features found within many modern ERPs also play an important role in enhancing labor management practices. The ability for managers to track employee attendance, work performed, and overall performance leads not just towards increased efficiency but also helps ensure fair treatment for all workers.
- Better Decision Making: Real-time data collection enables quick responses based on current circumstances rather than historical trends.
- Elevated Workforce Management: Automated tracking improves workforce scheduling while reducing administrative tasks related to manual data entry and calculations – meaning less paperwork, yay.
- Fairness: Precise record-keeping aids adherence to employment laws protecting employee rights while fostering trust between employers and employees through transparency.
In conclusion, we’re living in exciting times as we watch how technology revolutionizes the way we manage labor in manufacturing. It’s high time to join in and accept these transformations for a more efficient, equitable, and productive outlook.
Embracing tech in labor management is a game-changer for manufacturers. ERP systems offer real-time data, automating processes and boosting efficiency on the shop floor. They also promote fairness through accurate record-keeping and trust-building transparency. But despite these benefits, only 13.2% of plants use ERPs – it’s high time to seize this opportunity.
FAQs in Relation to Manufacturing Success With Labor Management
What are the benefits of labor management?
Labor management can boost productivity, lower costs, and improve work quality. It also promotes fair treatment and better communication between workers and managers.
How do you succeed in manufacturing?
Succeeding in manufacturing requires a mix of strategic planning, efficient operations, advanced technology like ERP systems, data-driven decisions, and effective labor management.
How do labor and management work together?
Laborers provide their skills while managers guide workflow. Together, they cooperate to reach production goals within set deadlines with optimum efficiency.
How successful were labor unions in improving working conditions?
Labor unions have played key roles in securing higher wages, safer workplaces, training opportunities, and worker rights over time despite declining membership numbers recently.
Conclusion
Our journey through the intricate landscape of labor management in the manufacturing industry has been eye-opening. One noteworthy aspect is the ebb and flow of union memberships, a significant factor that influences the dynamics within the workforce.
It’s essential to remember that the advantages of ERP systems extend beyond large-scale manufacturing plants; even smaller firms can harness their power to enhance productivity. The key lies in the ability to utilize real-time data provided by these systems to make immediate decisions that have a direct impact on overall performance.
In today’s world, inclusivity is not just a buzzword; it’s a fundamental aspect of achieving Manufacturing Success with Labor Management. Addressing wage disparities and actively promoting diversity within your organization is not only ethical but also crucial for creating a workforce that thrives. It’s about recognizing the value of every individual, regardless of their background, and ensuring that they have equal opportunities to contribute to the organization’s success. Labor unions, too, play a pivotal role at local levels by advocating for employee training and skills upgrading, a force that should not be underestimated.
Looking ahead, the path to success involves weaving together all these essential elements into a harmonious symphony on your shop floor. By recognizing the significance of union dynamics, harnessing the potential of ERP systems, fostering inclusivity, and collaborating with labor unions, you can orchestrate a manufacturing operation that resonates with efficiency, equality, and success, guided by the principles of smart labor management.